Drive In/ Drive Through Racks | Reno/ Sparks
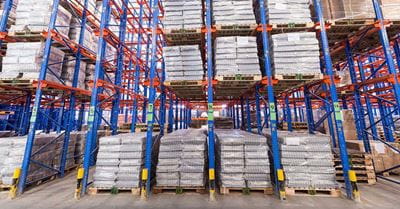
Raymond West is a West Coast supplier of warehouse storage solutions, including Drive In / Drive Through Racking systems. We are backed by one of the largest material handling equipment service operations in the West. Call us today at (775) 356-8383.
Effective warehouse management is largely based on making the most of storage space and ensuring convenient access to products. Two widely-used approaches for achieving this balance are drive-in and drive-through pallet racking systems. These systems provide unique advantages and cater to different storage requirements, but they possess a common goal of enhancing storage density by reducing aisle space. Grasping the distinctions between these systems is crucial for businesses looking to improve their warehouse operations.
Drive-In Pallet Racking Systems
Drive-in racking systems are defined by their deep storage lanes that enable lift trucks to drive directly into the rack structure to reach pallets of goods. These systems are created for high-density storage of homogeneous items with lower turnover. Drive-in racks consist of continuous rows of uprights and rails, with each lane accommodating multiple pallets situated one in front of the other.
The most prominent feature of drive-in configurations is that they have a single access point on the rack face, where lift trucks ingress and pick up pallets. This configuration supports a last-in, first-out (LIFO) inventory management system, where newly stored pallets are selected first, making drive-in racks perfect for storing non-perishable products.
Drive-Through Pallet Racking Systems
Drive-through pallet racking systems share similarities with drive-in designs but they have access points on both ends of the racking structure as opposed to just one. This allows forklifts to enter from one aisle to store or retrieve goods and egress from the opposite side. In contrast to drive-in solutions, drive-through racks facilitate a first-in, first-out (FIFO) inventory scheme, where the oldest items are picked first. This makes them suitable for facilities with a swift turnover rate or for warehouses that focus on stock rotation.
Increasing Warehouse Storage Density
Both drive-in and drive-through racking solutions excel at optimizing storage density by minimizing aisle space. Traditional racking solutions need spacious aisles for lift truck usability, but drive-in and drive-through designs can minimize the number of aisles needed in a facility. By enabling lift trucks to access goods from inside the rack footprint, these designs make more efficient use of the addressable capacity throughout the warehouse.
Minimizing aisle space results in enhanced storage capacity within the same footprint. Warehouses can maintain a larger number of products without increasing their physical capacity, making drive-in and drive-through racking systems budget-friendly solutions for businesses aiming to maximize their storage efficiency.
Choosing the Right System
When choosing between drive-in and drive-through pallet racking systems, warehouses must evaluate variables such as product particularities, turnover rate, and inventory handling demands. Drive-in racks are perfect for storing larger numbers of similar products with infrequent turnover, while drive-through options are ideal for businesses with a higher turnover rate or those that seek inventory rotation.
Drive In / Drive Through Rack Near Me
To learn more about your options, get in touch with a warehouse equipment professional at Raymond West today.Raymond's Reno / Sparks service operation includes all of Western Nevada, including Reno, Sparks, Carson City, Minden, Gardnerville, Incline Village, Virginia City, Indian Hills, Johnson Lane, Fernley, Fallon, Dayton, Silver Springs, Spanish Springs, Yerington, Genoa and Zephyr Cove.
Raymond West | Reno / Sparks Material Handling Equipment Supplier
975 Terminal Way
Reno, NV 89502
(775) 356-8383