Drive In/ Drive Through Racks | Long Beach
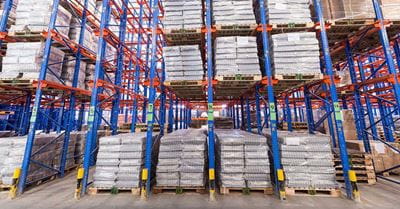
Raymond West is a West Coast supplier of warehouse storage solutions, including Drive In / Drive Through Racking systems. We are backed by one of the largest material handling equipment service operations in the West. Call us today at (562) 444-1222.
Efficient warehouse management depends primarily on making the most of storage space and maintaining accessibility to products. Two popular solutions for attaining this balance are drive-in and drive-through racking systems. Both systems offer distinct benefits and serve different storage requirements, but they share a common goal of boosting storage density by reducing aisle space. Comprehending the differences between these categories is vital for businesses seeking to enhance their warehouse operations.
Drive-In Pallet Racking Systems
Drive-in racking systems are characterized by their deep storage lanes that permit lift trucks to drive directly into the rack structure to retrieve palletized products. These systems are designed for high-density storage of homogeneous goods with lower turnover. Drive-in racks include continuous rows of rails and uprights, with each lane accommodating multiple pallets placed one in front of the other.
The most prominent benefit of drive-in configurations is that they have a uniform access point on the rack face, where lift trucks enter and retrieve pallets. This design facilitates a last-in, first-out (LIFO) inventory plan, where newly stored pallets are retrieved first, making drive-in racks ideal for stocking products without expiration dates.
Drive-Through Pallet Racking Systems
Drive-through pallet racking systems are similar to drive-in designs but they have entry and exit points on both sides of the rack as opposed to just one. This enables forklifts to enter from one side to store or retrieve products and egress from the other side. Different from drive-in solutions, drive-through designs facilitate a first-in, first-out (FIFO) inventory plan, where the oldest goods are accessed first. This makes them appropriate for operations with high product turnover or for businesses that prioritize product rotation.
Increasing Warehouse Storage Density
Both drive-in and drive-through racking solutions excel at maximizing storage density by cutting down on the need for aisle space. Typical storage systems require spacious aisles for forklift operability, but drive-in and drive-through racks can reduce the quantity of aisles needed in a facility. By enabling forklifts to pick goods directly from within the rack footprint, these systems optimize the use of available capacity within the warehouse.
Minimizing aisle space translates to enhanced storage capacity within the same area. Warehouses can maintain a greater volume of products without growing their physical capacity, making drive-in and drive-through racking systems cost-effective solutions for businesses aiming to optimize their storage capacity.
Choosing the Right System
When selecting between drive-through and drive-in designs, businesses must take into account factors such as product characteristics, product rotation, and inventory handling needs. Drive-in racks are perfect for storing larger numbers of homogeneous goods with low rotation, while drive-through types are perfect for operations with a higher inventory turn rate or those that seek product rotation.
Drive In / Drive Through Rack Near Me
To find out more about your options, reach out to a warehouse design professional at Raymond West today.Raymond West's Long Beach service area includes Long Beach, North Long Beach, Wilmington, San Pedro, Lomita, Torrance and nearby surrounding areas.
Raymond West | Long Beach Material Handling Equipment Supplier
Long Beach
(562) 444-1222