What is the best rack for product storage?
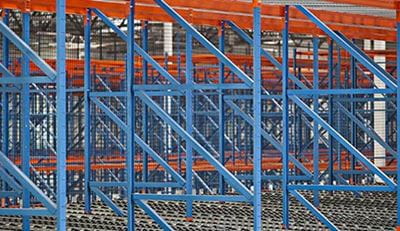
Efficient warehouse layouts frequently implement a variety of storage rack to accomodate the various speeds at which their Stock Keeping Units (SKUs) move.
Fast Moving SKUs
Often used for the 10% of the SKUs in the warehouse. Fast moving SKUs are often stored in a dense storage media such as the following:
- Bulk Stacking
- Pallet Flow
- Drive-in Racking
- Deep lane Radio Shuttle
Bulk Stacking in Warehouse has both pros and cons:
Pros of Bulk Stacking
- Inexpensive (no capital investment for the storage media beyond the warehouse square footage).
- Very dense storage method from a square footage point of view.
- Ideal for storage of dense and heavy products such as reams of paper, tins and cans of food, etc.
- Best for product that does not have an expiration date.
Cons of Bulk Stacking
- May crush or lean due to product instability
- Limited to 2 or 3 pallets high due to instability
- May not use the full storage height available in the warehouse. Not dense from cubic space point of view.
- Subject to honeycombing (loss of storage).
- Loss of space utilization.
- No rotation of product, therefore product may expire before it is discovered.
Pallet Flow Racking
Here are the pros and cons of Pallet Flow Racking:
Pros of Pallet Flow
- Rotation is automatic
- Great use of cube
- Good utilization with low honeycombing possible
- Increased warehouse productivity
Cons of Pallet Flow
- High capital investment (expensive)
- Loss of vertical cube due to pitch
- Needs maintenance over time
- Poor quality pallets may get stuck in a lane
Drive-in Racking
Drive-in Racking is one of the most misapplied racking styles. Although it has many benefits for the warehouse, if applied to unsuited SKUs, the negatives can outweigh the positives.
Pros of Drive-in Racking
- Very dense storage
- Only slightly more expensive than selective rack, very cost effective
Cons of Drive-in Racking
- Honeycombing can become problematic
- Stressful on the lift truck operator when lanes are deeper
- Subject to damage from forklifts
- Lost and expiring product can become a problem if not well managed
Pallet Radio Shuttle
Pallet Shuttle, or also called BT RadioShuttle or Pallet Runner or Pallet Mole, acts like pallet flow but instead of gravity, uses a little robot to move pallets in and out of the storage system.
Pros of Pallet Shuttle
- Very dense storage
- Can be up to 60 pallets deep
- Level, so no loss of vertical cube due to pitch
- Part of the movement is automated due to the use of the shuttles, therefore creates a highly productive warehouse (with reduced labor).
- Low honeycombing due to reorganization feature on some more advanced models
- Inexpensive compared to pallet flow, but more money than pallet flow
- Ideal for high value square footage such as in manufacturing (factories) and cold storage
Cons of Pallet Shuttle
- Requires at least 2000 pallet positions to be cost competitive to other storage methods such as pallet flow
- Some vertical cube is lost due to ~ 9″ high rails, therefore in lower ceiling warehouses it is harder to justify against bulk stacking.
Medium Moving SKUs
If your operation has 8 pallets of any particular SKU, a different style of storage is indicated. Medium moving SKUs are often stored in a simpler storage media such as the following:
- Double Deep, deep reach
- Push-back
- Single selective rack
Double Deep, Deep Reach
Working in double deep racking provides many benefits for medium moving SKUs.
Pros of Deep Reach
- Very inexpensive storage density: only slightly more expensive than single selective racking
- Provides good density with up to 88% space utilization of any particular SKU, assuming the rule of 4 is observed.
Cons of Deep Reach
- Requires a raised bottom beam limiting pallet trucks from pulling pallets at the bottom level.
- Deep reach lift trucks using a bottom beam cause a loss of 10″ to 12″ in vertical storage everywhere in the storage area.
- Otherwise, a deep reach truck requires a longer beam for straddling the pallet with the accompanying loss of storage down aisle – horizontal loss of storage cube.
- A specialized reach truck is required
- 50% selectivity is created by burying a pallet behind another pallet.
Push-back Rack
Push-back racking provides many benefits for medium moving SKUs, including:
Pros of Push-back Rack
- Increased storage density eliminating aisles
- Gravity faces the product forward, therefore ideal for use in pick aisles where case picks require regular replenishment
- May be loaded and unloaded by counterbalanced lift trucks, therefore reducing double handling from specialized lift trucks (such as in the case of Deep Reach trucks).
Cons of Push-back Rack
- At least 2.5 times more expensive than standard selective rack.
- Requires a wider aisle because the lift truck must line up with the storage slot and push squarely when storing and retrieving pallets.
Single Selective Racking
Single selective racking is one of the most versatile types of racking and can be used to store medium mover SKUs.
Slow Moving SKUs
Slow moving SKUs often represent up to a whopping 50% of SKUs stored in a warehouse but produce only 5% of the movement (sales). Therefore they are the most expensive product to store. However, many times, these slow SKUs are found in the same storage media as much faster moving SKUs, wasting precious space. Good storage media for slow moving SKUs are:
- Steel Shelving
- Vertical Lift Modules (VLMs)
- Vertical Carousels
Steel Shelving
Steel shelving is a popular style of inexpensive storage for slow movers. Here are the Pros and Cons:
Pros of Steel Shelving
- Inexpensive to buy
- Simple to set up (often does not require installation crews)
- Readily available (commodity item to buy)
- Modular; can be added to over time.
Cons of Steel Shelving
- Only uses the first 7 feet of the warehouse’ vertical cube. Huge loss in space.
- Usually set up for ground level picking, labor costs increase due to the speed at which a picker walks through a warehouse.
Vertical Lift Modules (VLM)
Vertical lift modules are a highly dense media for warehouse and point of use storage found in medical, aerospace and auto parts warehouses. As a storage method the are a few clear advantages and disadvantages.
Pros of Vertical Lift Modules
- Excellent use of vertical cube. Up to 90% space savings over steel shelving.
- Access controlled limiting who can pick from the VLM.
- Modular and can be increased in height over time.
- Flexible storage slots (tray height). Light curtains measure products going into the VLM and store the product in the appropriate slot based on size.
- Trays can be added as required
- Different trays can store different weight products
Cons of Vertical Lift Modules
- Although speeds have increased, taller machines can cause the picker to wait for a pick and therefore are best used for the slowest moving SKUs.
- Expensive (ROI can be long).
Vertical Carousels
Vertical carousels are a highly dense media for warehouse and point of use storage found in office, medical, aerospace and auto parts warehouses. As a storage method the are a few clear advantages and disadvantages.
Pros of Vertical Carousels
- Dense storage
- Good retrieval times and therefore useful for picking
- Less expensive than some VLMs.
Cons of Vertical Carousels
- The size of each storage bin is fixed at the time of purchase
- The height of the machine is fixed at the time of purchase
- The weight of each bin must be similar to not let the machine fall out of balance
Conclusion
As you can see, if you are planning a new warehouse but have only one type of storage planned – Selective Racking – you are probably missing an opportunity to design the warehouse with built-in density and productivity.
Let us know your thoughts about this article. We love to hear from our readers.