Conventional-Opportunity-Fast Charging Batteries
Conventional-Opportunity-Fast Charging Batteries
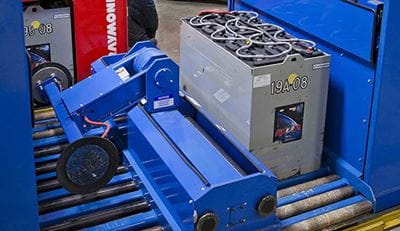
What is the difference between conventional, opportunity and fast charging forklift batteries?
There is no “one size fits all” battery and charger system for electric forklifts. Conventional, opportunity and fast charger systems offer benefits and limitations. An electric forklift fleet is only as good as the battery and charger system it uses.
What is conventional charging of a forklift battery?
- Batteries are charged at rates of 16-18 A / 100 Ahrs
- Batteries take an average of 8 hours to fully recharge the battery
- Conventional charging ideal for one shift operations
- For multi-shift operations (2 or 3 shifts), more than one battery per truck is needed
- Conventional chargers charge the battery to a 100% state of charge (SOC) on a daily basis
Conventional charging is ideal for one-shift applications where no battery changing is required. Conventional charging requires that the battery is charged over an 8-hour period, rests and cools down for another 8 hours, and is used (discharged) over an 8 hour shift. The battery is run during the day to 20% remaining capacity, re-charged in the evening to 100% state of charge (SOC) and then the next day it is cooled down and is ready to be used. Conventional chargers charge the battery to a 100% state of charge (SOC) on a daily basis, which involves considerable gassing to bring the battery to its specific gravity.
In multi-shift operations (two or three shifts) users need at least 2 batteries per truck, which requires battery changes. This means changing batteries every 8 or so hours, requiring labor, time and risk of injury. While there are efficient ways to change batteries, there are also downsides:
- Battery changing equipment is expensive
- Safety concerns
- Environmental concerns due to dropping the battery or spilling electrolyte
- Productivity can be negatively impacted
- Potentially shorter run times
- Battery replacements earlier than expected
- A chance of higher repair costs
What is opportunity charging of a forklift battery?
- Batteries are charged at rates of 25 A / 100 Ahrs
- Batteries are charged at every possible opportunity (i.e. breaks, lunch, shift changes)
- Batteries take an average of 4 – 6 hours daily total to fully recharge the battery
- Opportunity charging is a good choice for extended shift operations or two-shift operations where battery changing can be eliminated
- Opportunity charging is good for multi-shift operations and for companies that have space to install strategic charging stations
- Due to the frequent charging and in order to limit battery gas generation, opportunity chargers are normally set to charge a battery up to 80%-85% SOC throughout the day and back to 100% only once a day (during night hours).
This entails placing chargers in centralized charging areas to maintain hydrogen concentrations that stay below OSHA limits.
If you have a high energy consumption single shift application or frequently need to run the forklift for more than 1 shift daily or the shift is extended past 8 hours, an opportunity charging system could be a
good fit for you. Opportunity Charging is completed during breaks, between shifts, and any short period of time when the battery is not being used.
Opportunity chargers are programmed to shut off at up to 80%-85% SOC throughout the day the work shifts limiting the cycles used, while controlling the amount of heat generated; and charged back to 100% once a day, usually during the night hours. There are limitations to opportunity changing systems; opportunity charging will not be able meet the demands required in high energy consumption applications or in most 3 shift applications where the trucks are pushed to their limits.
If your operation is conducive to opportunity charging, there are some additional factors to consider:
- There is an infrastructure cost to locate chargers near break rooms or work areas so it’s convenient for operators to charge at every opportunity.
- You will have to enforce the discipline to charge during breaks and lunches so the truck can make it through the shifts.
- You will need to provide nightly down time to restore the battery to 100% SoC between shifts
- Trucks must be plugged in for a consistent 12 hours to receive an equalization weekly
Even with these factors, opportunity charging could save your company money over the long term by using fewer batteries, eliminating battery change out equipment, and increasing productivity by removing the lost time required for each battery change.
What is fast charging of a forklift battery?
Batteries are charged at rates of 40+ A / 100 Ahrs
Batteries are charged at every possible opportunity (i.e. breaks, lunch, shift changes)
Batteries take an average of 2 -3 hours daily total to fully recharge the battery
Batteries are charged to 80%-85% SOC on a daily basis thus eliminating any unnecessary gassing
Fast charging is good for three-shift / heavy use operations
Fast chargers charge a battery up to 80%-85% SOC throughout the day and back to 100% once a week
If you are running a high production facility where the machines have extreme energy consumption environments or if you are a 24/7 operation a fast charging system may be best for you. Fast charging has a higher charging rate and more frequent charging throughout the day, means that you only require a single battery per truck. The battery can partially charge up during breaks or in-between shifts. This eliminates the need for extra batteries and for battery change-outs between shifts. Operations with limited space will also benefit from fast-charging as you no longer need battery change-out rooms.
Fast charge batteries are designed to minimize temperature rise while maximizing and charge acceptance, meaning they are able accept a higher charge rate while also reducing the operating temperatures of the battery. Fast charge batteries are commonly equipped with dual Intercel connectors, and dual cables with dual connectors for applications requiring charging amps in excess of 300A.
With fast charging, the batteries are only charged to 80%-85% SOC on a daily basis thus eliminating any unnecessary gassing. This eliminates the need for additional batteries and greatly improves truck driver productivity because the time spent changing batteries in two and three shift applications are eliminated. The battery utilization factor jumps to a full 100% (full utilization of the asset) with fast charging.
Battery manufacturers along with PDS also require that all fast charge batteries must be equipped with temperature feedback. Some other accessories should be considered, including a single-point watering system with water level indicator and an optional battery monitor.
No matter the charge rate and system, the lead acid battery will need to perform what is known as an equalization charge once per week. Weekly equalizations to keep batteries healthy balances the specific gravity or acid consistency of the battery and prevents the acid from concentrating at the bottom of the battery, reducing the possibility of battery damage, while also ensuring maximum output efficiency.