Belt vs. Roller Conveyors: Which Is Best for Your Application?
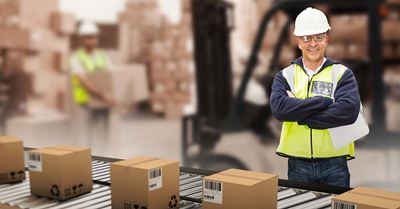
Selecting the right conveyor system is essential for optimizing material handling operations. Understanding these differences ensures businesses invest in the right solution to streamline workflows and improve productivity.
In the intricate dance of modern material handling, conveyors play the role of the unsung hero. Whether you’re moving products through an assembly line or facilitating warehouse operations, choosing the right conveyor system is critical. Two of the most common options are belt and roller conveyors, each with unique strengths suited to different applications. But how do you decide which one is the perfect fit for your needs? Before diving into comparisons, it’s important to understand what sets belt and roller conveyors apart. Belt conveyors consist of a continuous belt that runs over pulleys and is powered by a motor. They’re typically used for transporting goods over longer distances or when items need to be supported fully. Best For: Smooth and consistent transportation of products, especially smaller or irregularly shaped items. Common Industries: Food processing, packaging, and manufacturing. Roller conveyors, on the other hand, use a series of rollers—driven by gravity, motors, or manual force—to move items along a flat surface. Depending on the design, they may be powered (motorized rollers) or non-powered (gravity-fed). Best For: Handling heavier loads or items with flat bottoms. Common Industries: Warehousing, logistics, and automotive manufacturing. The nature of your product is often the first determining factor in selecting a conveyor system. Belt Conveyors: Ideal for delicate or small items that require consistent support. For example, think of small electronic components, packaged goods, or powders. Their smooth surface ensures items won’t fall through gaps, making them a safer choice for irregularly shaped items. Roller Conveyors: Better suited for sturdy, flat-bottomed items like boxes, pallets, or heavy machinery parts. Their modular design allows for easy handling of bulky loads. The length of your operation and the required speed of material flow can also guide your choice. Belt Conveyors: Shine over long distances or when consistent speed is a priority. For example, a belt conveyor is perfect for moving goods from one end of a factory to another without interruptions. Roller Conveyors: More suitable for shorter distances or sections where items may need to stop and accumulate, such as in sorting or shipping areas. No equipment is maintenance-free, but understanding the upkeep involved is crucial. Belt Conveyors: Require regular inspection to prevent misalignment, belt wear, or tears. The entire belt might need replacing over time, which can be costly. Roller Conveyors: Tend to have fewer moving parts, making them easier to maintain. However, if a roller becomes damaged, it can disrupt the entire system until replaced. Your choice of conveyor should align with the growth and adaptability of your operation. Belt Conveyors: While highly effective, they can be less modular, making adjustments or expansions more challenging. Roller Conveyors: Their modular design allows for greater flexibility. You can easily add or remove sections as needed, making them an excellent choice for evolving workflows. Cost is always a factor when investing in new equipment. While belt conveyors might have a higher upfront cost due to their motorized components and continuous belts, they can save money in certain scenarios by reducing downtime and increasing efficiency. Roller conveyors, with their simpler design, may be more affordable initially, but the savings can vary depending on your specific needs. In some operations, the best solution isn’t choosing one over the other but integrating both systems. For example, a facility might use belt conveyors for transferring small products and roller conveyors for handling larger, bulkier items at loading docks. A hybrid approach ensures optimal performance across the entire workflow. Selecting between belt and roller conveyors isn’t a one-size-fits-all decision. It’s about aligning the system with your operational needs, product types, and long-term goals. By carefully considering factors like product nature, distance, speed, and maintenance, you can choose the conveyor system that propels your business toward greater efficiency. To learn more about conveyor options, contact a warehouse automation expert at Raymond West today.
Understanding the Basics
Belt Conveyors
Roller Conveyors
Key Considerations: Choosing the Right System
1. Type of Product
2. Distance and Speed
3. Maintenance Requirements
4. Flexibility and Scalability
Cost Analysis
When to Combine Both Systems
Making the Final Decision