Automated Palletizing: Efficiency Gains for High-Volume Warehouses
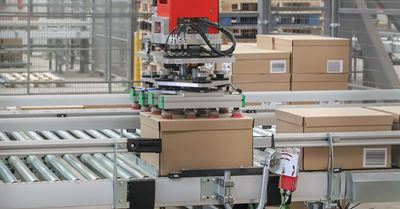
Automated palletizing is transforming high-volume warehouse operations by enhancing efficiency, precision, and safety. These systems—ranging from conventional palletizers to advanced robotic solutions—streamline the stacking and storage process, reducing errors and increasing throughput.
In the fast-paced world of high-volume warehouses, efficiency isn’t just a goal—it’s a lifeline. With the constant pressure to move goods quickly and accurately, warehouse managers are always searching for ways to streamline operations. Enter automated palletizing: a game-changing solution that promises to revolutionize how warehouses stack, store, and ship products. Automated palletizing systems have emerged as a key player in warehouse automation, offering unprecedented levels of speed and precision. But what exactly makes these systems so effective, and how can they address the unique challenges of high-volume facilities? Automated palletizing involves the use of machines or robots to stack products onto pallets for storage or transport. Unlike manual palletizing, which relies on human labor, automated systems use advanced algorithms, sensors, and mechanical precision to arrange products in optimal configurations. These systems come in two main types: Conventional Palletizers: Use mechanical components like conveyors and sliding plates to organize items. Robotic Palletizers: Employ robotic arms equipped with grippers or suction cups for more flexible and dynamic stacking. Regardless of the type, the goal remains the same: to maximize efficiency while minimizing errors and physical strain on workers. High-volume warehouses often deal with thousands of pallets daily. Manual palletizing simply cannot keep up with this demand. Automated systems, on the other hand, can handle hundreds of cycles per hour, ensuring that products move through the supply chain seamlessly. Think of it as upgrading from a single-lane road to a multi-lane expressway—bottlenecks are virtually eliminated, and productivity soars. Human error is an inevitable part of manual processes. Products may be stacked unevenly or in configurations that risk damage during transport. Automated systems excel in precision, ensuring that each pallet is stacked to exact specifications. This consistency reduces the likelihood of product damage, making automated palletizing particularly valuable for fragile goods or irregularly shaped items. Manual palletizing is labor-intensive and physically demanding, often leading to worker fatigue or injuries over time. By automating the process, warehouses can reallocate their workforce to less strenuous, higher-value tasks. Moreover, automated systems remove the risk of injuries associated with heavy lifting and repetitive motions, creating a safer working environment. As businesses grow, so does the demand for faster and more efficient operations. Automated palletizing systems can scale with your needs, accommodating higher volumes without requiring significant changes to your workforce or facility layout. Modern automated palletizers are designed to integrate seamlessly with WMS software, enabling real-time tracking and data analysis. This integration provides valuable insights into operations, from inventory levels to shipping schedules, empowering managers to make data-driven decisions. Upfront Costs: One of the most frequently cited barriers to automation is the initial investment. While automated palletizing systems do require a significant upfront cost, their long-term benefits—such as reduced labor expenses, lower error rates, and increased productivity—often result in a compelling return on investment (ROI). Complexity of Implementation: Transitioning to automation can feel overwhelming, especially for facilities with legacy systems. However, many providers offer tailored solutions and support during implementation, ensuring a smooth transition. Additionally, modular designs allow warehouses to adopt automation incrementally, minimizing disruption. Adaptability to Different Products: Warehouses handling a wide variety of products may worry about whether automated palletizers can accommodate diverse shapes and sizes. Robotic palletizers, in particular, excel in versatility, with the ability to adjust grippers and stacking patterns dynamically. The decision to invest in automated palletizing ultimately depends on your warehouse’s specific needs and goals. High-volume facilities with tight timelines and diverse product ranges stand to benefit the most. However, even smaller operations can gain a competitive edge by automating their palletizing processes. When evaluating options, consider factors such as: Your current and projected workload. The types of products you handle. Integration with existing systems and processes. Budget and expected ROI. Automated palletizing is more than just a technological upgrade—it’s a strategic investment in the efficiency and scalability of your warehouse operations. By improving speed, accuracy, and safety, these systems empower businesses to meet the demands of a rapidly evolving supply chain landscape. If your warehouse is ready to embrace the future, automated palletizing could be the key to unlocking new levels of productivity and profitability. To learn more about palletizing solutions, get in touch with an automation expert at Raymond West today.
What Is Automated Palletizing?
Key Benefits of Automated Palletizing for High-Volume Warehouses
Drastic Increases in Throughput
Enhanced Precision and Consistency
Labor Savings and Safety Improvements
Scalability for Growing Operations
Integration with Advanced Warehouse Management Systems (WMS)
Addressing Common Concerns
Are Automated Palletizing Systems Right for Your Warehouse?
Building a More Efficient Future