Using Lean Principles to Streamline Warehouse Processes: Unlocking Efficiency, One Step at a Time
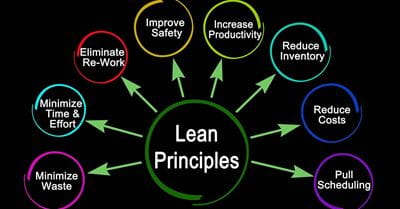
Warehouses are fast-paced environments, but hidden inefficiencies can slow operations and drain profits. Embracing Lean isn’t just about cutting costs—it’s about creating a smarter, more agile warehouse that benefits both employees and the bottom line.
The modern warehouse is a hive of activity—employees picking, packing, and shipping orders in a race against the clock. But beneath the surface of this frantic pace often lies a tangle of inefficiencies: unnecessary movement, wasted resources, and processes that do more to slow things down than speed them up. Enter Lean Principles, a time-tested methodology born in manufacturing but perfectly suited for warehouses striving to optimize operations. By focusing on eliminating waste and fostering continuous improvement, lean principles offer a pathway to smoother workflows, happier employees, and healthier profit margins. Lean principles, originally developed by Toyota, focus on maximizing value while minimizing waste. In the context of warehousing, waste can take many forms: excess inventory, inefficient layouts, or even overworked employees. To tackle these challenges, Lean thinking emphasizes three core concepts: Value Stream Mapping: Understanding the flow of materials and information to identify bottlenecks. The 8 Wastes: Eliminating non-value-adding activities like overproduction or unnecessary motion. Continuous Improvement (Kaizen): Encouraging ongoing small changes for big cumulative results. Think of your warehouse as a river, with goods flowing from one end to the other. Is the flow smooth, or are there snags along the way? Value Stream Mapping helps you visualize your operations, pinpointing delays and inefficiencies. For example, in a high-volume fulfillment center, mapping might reveal that workers spend 30% of their time walking between shelves and packing stations. By rearranging the layout, this wasted motion can be reduced, saving hours of labor each week. Lean identifies eight categories of waste (often remembered by the acronym TIMWOODS): Transportation: Minimize unnecessary movement of goods. Use conveyors or automated guided vehicles (AGVs) to streamline material transport. Inventory: Adopt just-in-time (JIT) principles to avoid overstocking. Motion: Reduce excessive bending, stretching, or walking for employees. Ergonomic workstations can make a huge difference. Waiting: Ensure that equipment and personnel are always ready to act. Downtime is a silent profit killer. Overproduction: Produce or pick only what’s needed, when it’s needed. Overprocessing: Avoid doing more than what the customer requires. Defects: Implement quality control processes to reduce rework. Skills Underutilization: Engage employees in problem-solving and decision-making to harness their full potential. The beauty of Kaizen lies in its simplicity. Employees at all levels contribute ideas for improvement, fostering a culture of innovation. For instance, one warehouse might introduce a simple color-coding system for inventory bins, making it easier to identify products at a glance. Over time, such small tweaks accumulate, creating significant efficiency gains. Implementing Lean principles isn’t just about technology and workflows—it’s about people. Employees who feel valued and empowered are more likely to embrace change. Start by involving your team in brainstorming sessions. Ask open-ended questions like, “What slows you down the most during your shift?” or “How can we make this process easier?” By giving employees a voice, you’ll uncover practical insights while fostering a sense of ownership. A mid-sized distribution center in Southern California’s Riverside County was struggling with late shipments and frustrated employees. By applying Lean principles, the company revamped its picking process using value stream mapping. They introduced a pick-to-light system, reducing errors and cutting picking times by 40%. Simultaneously, a Kaizen event led to the redesign of their loading docks, eliminating bottlenecks during peak hours. Within six months, on-time shipments rose from 85% to 98%, and employee satisfaction improved dramatically. Lean transformations are not without hurdles. Resistance to change is common, especially when it disrupts familiar routines. To navigate this, focus on clear communication. Share the “why” behind every change, and celebrate small wins along the way to build momentum. Applying Lean principles to your warehouse isn’t just about cutting costs—it’s about creating a workplace that works smarter, not harder. By eliminating waste, optimizing processes, and fostering a culture of continuous improvement, you can unlock your warehouse’s full potential. Remember, Lean is a journey, not a destination. Start small, stay consistent, and watch as even the smallest changes ripple outward to create a wave of efficiency. After all, the smoothest rivers are those that flow without obstruction—just like your warehouse should.Understanding Lean: More Than Just a Buzzword
Applying Lean to Warehouse Processes
1. Value Stream Mapping: Seeing the Bigger Picture
2. Reducing the 8 Wastes
3. Implementing Kaizen: Small Steps, Big Impact
The Human Element: Why Buy-In Matters
Real-Life Success: A Case Study
Overcoming Challenges: What to Expect
Summing Up The Lean Advantage