Applying OSHA Fall Protection Rules in Your Warehouse
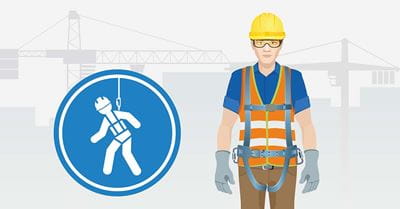
Understanding and adhering to OSHA's fall protection rules in warehouses is crucial for ensuring employee safety and compliance with regulations aimed at preventing workplace injuries and fatalities.
The Occupational Safety and Health Administration (OSHA) sets rigorous standards for fall protection in warehouses to ensure the safety and well-being of workers. Falls are a leading cause of workplace injuries and fatalities. Warehouses, with their elevated storage areas and busy work environments, are particularly susceptible to such risks. Compliance with OSHA's fall protection regulations is not only a legal obligation, it’s also a crucial step in protecting your employees. It’s important to understand the entire scope of these rules, and then address them with a policy and compliance plan that is based on best practices. OSHA's regulations for fall protection are detailed in several standards, most notably 29 CFR 1910 for general industry and 29 CFR 1926 for construction. For warehouses, the general industry standards are typically most relevant. Key requirements include: ● Fall Protection Plan: Employers must develop a comprehensive fall protection plan. This plan should identify potential fall hazards, outline procedures for preventing falls, and specify the fall protection systems to be used. ● Guardrails: When employees work at heights of 4 feet or more, OSHA mandates the use of guardrails. These should be 42 inches high, with a mid-rail at 21 inches, and capable of withstanding a force of 200 pounds. ● Personal Fall Arrest Systems (PFAS): For areas where guardrails are not feasible, PFAS are required. These systems include a full-body harness, anchorage, and connectors. The system must be capable of supporting at least 5,000 pounds per employee attached. ● Training: Employers must provide fall protection training to employees. This training should cover the proper use of fall protection systems, identification of fall hazards, and procedures to follow in case of a fall. ● Inspection and Maintenance: Fall protection equipment must be regularly inspected and maintained. Any equipment showing signs of wear, damage, or degradation must be removed from service immediately. ● Floor Openings: Openings in floors, such as skylights or pits, must be covered or guarded to prevent accidental falls. ● Ladders and Scaffolding: Proper use and maintenance of ladders and scaffolding are essential. Ladders should be inspected for defects before use, and scaffolding must be erected and used according to OSHA standards. To effectively comply with OSHA's fall protection standards, warehouses should consider implementing some of these best practices: ● Risk Assessment: Conduct a thorough risk assessment to identify all potential fall hazards within the warehouse. This includes evaluating elevated storage areas, loading docks, and other high-risk zones. ● Engineering Controls: Prioritize engineering controls to eliminate fall hazards. This includes installing permanent guardrails, using safety net systems, and designing safer work platforms. ● Administrative Controls: Implement administrative controls such as job rotation, supervision, and work scheduling to minimize time spent at heights and reduce fatigue. ● Regular Training: Establish a robust training program that includes initial and refresher courses. Training should be practical, hands-on, and tailored to the specific needs of the warehouse environment. ● Equipment Management: Maintain an inventory of fall protection equipment and ensure it is regularly inspected and replaced as necessary. Keep detailed records of inspections and maintenance activities. ● Emergency Procedures: Develop and communicate clear emergency procedures for rescuing workers in the event of a fall. Conduct regular drills to ensure employees are prepared for such scenarios. ● Continuous Improvement: Regularly review and update fall protection policies and procedures. Solicit feedback from employees and safety professionals to identify areas for improvement. ● Compliance Audits: Perform regular compliance audits to ensure that fall protection measures are being followed correctly. Use audit findings to address any deficiencies promptly. Sticking to OSHA's fall protection standards is essential for creating a safe warehouse environment. If you would like to review your current safety practices or need help developing policy and procedures, contact a warehouse expert at Raymond West today.What Are OSHA’s Fall Protection Requirements?
Best Practices for Compliance
Review Your Plan with a Warehouse Safety Expert