Why You Should Be Considering Goods-to-Person Automation
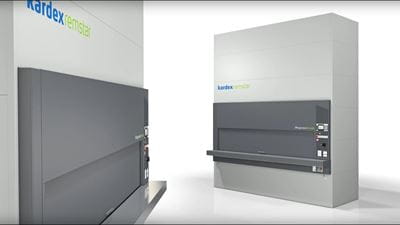
Many fulfillment operators are turning to Goods-to-Person (GTP) systems to meet e-com and just-in-time ordering requirements.
Ask any warehouse manager, and they will tell you the pressure to deliver goods faster is greater than ever before. Increased demand for just-in-time ordering and the rise of e-commerce merchants are some of the reasons for this shift. Many fulfillment operators have turned to Goods-to-Person (GTP) systems to meet those needs.
Person-to-Goods fulfillment is the traditional method of filling orders and typically involves sending workers to different zones to find products. While simple, this type of fulfillment strategy is highly inefficient because of the amount of time the employee spends going to and from stocking locations. Some productivity gains can be achieved by assigning workers to one zone which cuts down on foot and equipment traffic but doesn't go far enough to meet the needs of today's customer expectations.
Goods to Person (GTP) eliminates much of the walking and human intervention from the process, resulting in error reduction as well as massive efficiency gains. Automated Storage and Retrieval Systems retrieve goods from shelves and deliver them to an order picker's workstation, placing items in assigned totes or trays depending on size. Goods to person autonomous mobile robots move pods to a pick and pack station. As a result, both AS/RS and GTP AMR substantially reduce, but not totally remove, foot traffic and walking, and they also substantially increase productivity rates.
Key benefits of GTP systems are:
- They substantially reduce labor costs by reducing employee time spent traveling to and from product locations in the warehouse
- They greatly reduce pick errors
- Warehouses achieve better throughput times, improving customer experience
- Ergonomically designed pick stations offer improved employee comfort and safety
- Fewer forklifts are needed, reducing equipment and maintenance costs
So, what are the GTP systems that are most commonly used today?
Vertical Carousel
Vertical carousels are becoming more popular as a warehouse space-saving solution. They work by attaching a series of trays to a rotating chain that loops around both backwards and forwards like a 'Ferris Wheel.' Although each system has its own set of add-ons, the basic concept of each unit remains the same: the vertical carousel can deliver items to a surface with the push of a button.
Horizontal Carousel
Horizontal carousels have an advantage over vertical carousels in that they can store and deliver larger, heavier items. They usually have more than one unit installed so that they can consistently dispense items. They operate in the same way as a vertical carousel, but instead of rotating towards the ceiling, they rotate horizontally through the length of the unit.
Vertical Lift Module
VLM technology is the most adaptable because it can automatically adjust to changes in inventory. The unit is designed to handle a wide range of units, from large to small. Because each tray can be customized, it's simple to maximize the space occupied by each item of inventory.
Robotics
The majority of robotic solutions are available in two types of configurations: floor robots and robotic shuttles. Floor robots were created with the intention of delivering items to the picker from portable storage units. Once the item has been selected from the robot's storage, the robot will return to its original location in order to maximize space and speed.
Robotic shuttles differ in that they are built on rails and can retrieve cases, totes, or trays from shelving along the built-in rails. Both solutions are scalable in the sense that they allow for increased productivity with minimal structural investment by simply increasing the number of robots.
Talk To A GTP Expert
If you'd like to learn more about good-to-person technology and explore options for your warehouse, give us a call today! Raymond West has a team of automation experts that can help with just about any application.