Optimize Before You Automate
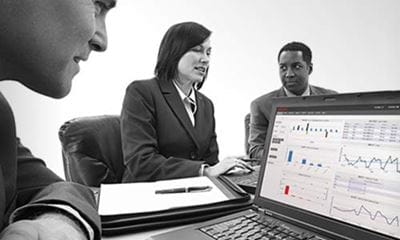
Many organizations jump headlong into warehouse automation projects based on assumptions, not hard data. Warehouse optimization can arm you with the data you need for building rock-solid ROI models.
Automation can fundamentally transform your warehouse by slashing your costs, scaling up your productivity, reducing mistakes and making you a leaner and meaner operation. However, to truly take advantage of automation, you need to know some things. Where are you currently most inefficient? How do your labor costs stack up against others in your industry? Where should you apply automation technologies to get the best return on your investment?
In other words, you should have an absolute understanding of what needs to be fixed before you try to fix anything.
Few businesses stop to truly research these questions before jumping into automation projects. As the expression goes, you “can’t manage what you don’t measure”. This is especially true in material handling, where combinations of human labor and machines make for complex cost and productivity analysis.
Optimization For Insight
Before taking on massive automation projects, warehouse operators should take a step back and completely optimize their operations. Optimization reveals the gaps, tells you where you are most inefficient, and gives you a baseline to work from.
Optimization reports can give you deep insight into what your workers are doing every day, how productive they are, how much of your equipment gets utilized every shift and to what extent, how your battery life affects productivity, and much, much more.
Between labor management tools, warehouse management systems, telematics, and other systems you can establish a solid baseline. From that baseline, you can identify opportunities to optimize your fleet and labor. Better yet, that baseline will help you develop an automation plan that is built on real numbers, not speculative ROI models that are full of assumptions.
Facility Automation
Once you’ve optimized, you can map out your automation projects, prioritizing the least efficient human processes first, building ROI models for each, and measuring your results over time. Automation does not fully replace human labor, it maximizes human contribution.
Despite what you may hear from automation equipment vendors, automation won’t solve every problem in your warehouse. There will be processes that are better left to realignment of labor and equipment rather than automation.
Smart warehouse operators look at automation as an iterative process, gradually enhancing and replacing human processes over time. By taking projects in bite-sized chunks, you can maintain productivity, minimize disruption and scale your organization efficiently over time.
Talk To An Expert
If you’re considering an automation project and would like help with analyzing and optimizing your warehouse, contact Raymond West today at (562) 944-8067.