Is It Time To Upgrade Your Order Picking System?
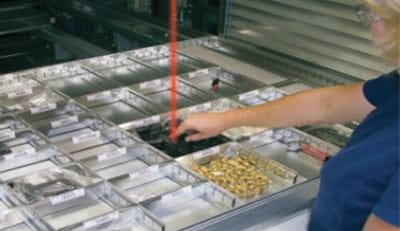
Advanced new technologies for batch picking and multi-order picking give warehouse operators the opportunity to eliminate errors, reduce costs, and greatly enhance productivity. But which technologies will give you the biggest bang for your buck?
E-com is driving a quantum shift in the way that warehouses work. Consumers now demand more SKUs, greater product variation and lightning fast delivery. This demand is not only putting pressure on available warehouse space, it's also driving operators to rely heavily on piece picking and case picking.
Rising warehouse costs, paired with labor intensive and error-prone picking methods are causing many operators to re-evaluate their picking systems.
Luckily, advanced new technologies for batch picking and multi-order picking are giving warehouse operators the opportunity to eliminate errors, reduce costs, and greatly enhance productivity. But which picking technology will give you the biggest bang for your buck? And is it even the right time to adopt a new technology, or should you hold off until these systems are a bit more mature?
The answer is yes, it's the right time. In fact, we are nearing the top of the adoption bell curve. At this point, warehouses that are still using paper or RF systems are at a competitive disadvantage, particularly in batch picking operations.
Although batch picking for several orders simultaneously is highly efficient, it also increases pick error rates substantially. Among the problems with batch picking are order mis-fills where one customer gets something they didn't order and another doesn't receive the item they ordered. Not only is this a costly error to resolve, it also results in an extremely negative customer experience. On average, batch picking operations have a 25% greater mis-fill rate than other types of picking styles.
Thankfully, there are several technologies that can assist with batch picking accuracy and speed. Chief among them are voice picking and pick-to-light systems.
Voice picking delivers pick instructions to workers via a headset, advising them of which aisle and bay to proceed to, which product to pick, the quantity of each item and which customer.
Pick-to-light is better suited for high speed picking in warehouses with a lower SKU count or a very localized picking layout. Quite often, it’s a better choice for zoned picking operations. The more pickers you have, the more cost effective pick-to-light becomes.
In general, a new picking system can be a substantial investment up front. However, once you start factoring picking speed improvements and error reduction, it’s not very hard to build a return-on-investment (ROI) model with a short payback period and attractive returns going forward.
If you consider the cost of an average mis-pick, it’s easy to see why there’s a compelling business case for advanced picking systems. A 2012 study showed that the average cost of a mis-pick was $22 per case before adding on less tangible costs like re-handling labor, re-delivery costs, and so on. The true cost of a mis-pick can often be as high as $100 per case.