Modernize Your Dock And Improve Your Bottom Line
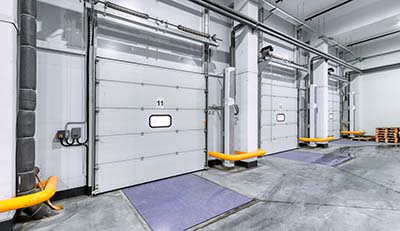
Is your loading dock a safe and efficient product transit hub, or is it just a "series of holes" in the back of your warehouse? Here's how to use the latest technology to improve safety, increase efficiency and make your dock the cornerstone of your operation.
When you reduce a warehouse operation to its fundamentals, it has two primary functions: storing goods, and moving those goods in and out of the facility. Many warehouse operators allocate substantial budgets to warehouse automation and density efforts, but few pay the same kind of attention to their loading dock.
The dock is the busiest and most congested area of the warehouse. Eliminating even the smallest of bottlenecks at your dock can add up to substantial cost reductions over time.
Saving your drivers a few seconds in different parts of their daily routines may not sound like a big deal, but over the course of a day that adds up to minutes, and over a year it translates to several days of labor for each employee. Multiply that by your number of operators and shifts, and there’s usually an opportunity for substantial efficiency gains.
And then there’s safety. Your dock is a high traffic, high risk area that should be addressed with ongoing operational assessment and vigilance. The loading dock is also your warehouse’s main point of interaction with the outside world. You are responsible not only for the safety of your own employees, but for the well being of everyone that transacts with your facility.
By implementing multiple safety improvement and cost reduction programs over time, you can gain substantial efficiencies from your dock operations while improving your safety record, enhancing your employee satisfaction and reducing your potential liability exposure.
Automatic Vehicle Restraints
Automatic restraints increase both safety and efficiency at the loading dock by automatically engaging when a trailer is in position. Not only do they save time by eliminating the need for employees to physically secure trailers, they also make unscheduled dock departures and trailer creep impossible. The likelihood of serious injury from landing gear failure and trailer upending are also reduced because automatic restraints generally restrict vertical movement of the ICC bar and the trailer.
Light Communication Systems
Light systems provide visual confirmation of the status of restraints and levelers, generally through red and green “stop and go” lights. Forklift operators have restricted visibility as they drive in and out of trailers with loads in their view path, so light communication systems are mounted in multiple areas, including door corners and at floor level.
Interlock Systems
Most docks have individual levelers, doors and vehicle restraints that operate independently of each other. An interlock control system ties all of these components together so that procedural steps are never missed and they’re always done in the right sequence.
For example, a control system can be set up to disable leveler and door engagement until an automatic vehicle restraint has been set. Once the restraint is in place, it then allows the overhead doors to be opened and finally enables operation of the dock leveler.
Hazard Detection and Warning
On average, more than 30,000 forklift pedestrian accidents are reported to OSHA every year. While blue lights projected in front of and behind lift trucks to alert pedestrians have become fairly common, these systems aren’t very effective when drivers are going in and out of trailers at the dock, or when approaching blind intersections.
You can equip your dock with additional systems that detect both human and forklift activity within trailers and at busy forklift drive path intersections. These stationary systems will display a blue light when a forklift or pedestrian is detected, warning both approaching forklift drivers and pedestrians of a hazard.
LED Lighting
LED lighting provides superior illumination and can cut energy costs by more than 50% compared to traditional lighting solutions. LED options are great for spot lighting the inside of trailers, flood lighting for dock exteriors, and high bay lighting to keep your dock area brightly lit and safe.
LED lighting systems can also be equipped with sensors that will dim or shut lights off during periods of inactivity.
HVLS Fans
Managing the airflow within your facility enhances employee comfort and reduces energy costs. HVLS fans can lower temperatures as much as 15 degrees during hot weather and reduce energy costs by as much as 30% during the winter months.
Don’t Wait Until It’s Too Late
All too often, warehouse operators implement comprehensive dock safety measures only after a serious accident puts them under the microscope. A better approach is to implement a preventative incremental improvement plan, gradually introducing dock modernization initiatives over a period of 2-3 years.
Ongoing improvement processes also have a hidden benefit: safety enhancement and dock cost reduction measures are reviewed quarter after quarter, keeping these types of initiatives top of mind for management and employees.
If you’d like to review the latest in dock safety and efficiency, contact a warehouse efficiency expert at Raymond West today!