Pick To Light Solutions | San Francisco Bay Area
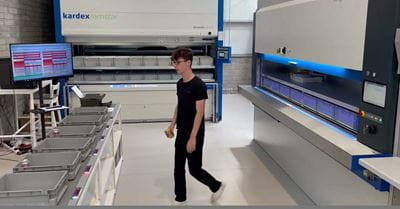
Raymond West is a Bay Area warehouse automation consultant. We design, install and maintain order picking solutions.
Call us today at (800) 675-2500.
Businesses that run complex warehouse and distribution operations are always on the lookout for innovations that can increase productivity and minimize costs. These businesses generally perform thousands of order picks per hour, and technologies that offer greater pick accuracy can result in substantial cost decreases and improved client satisfaction.
Over the last few years, many new order picking innovations have been introduced to the market. Amongst them, "pick-to-light" technology stands apart for its potential to dramatically increase warehouse performance while almost eradicating pick errors.
How Pick to Light Works
Workers scan a barcode on a tote or picking container which is an encoded adaptation of an individual client order. Based upon the shipment, the system will instruct an operator to select a product from a specific bin.
Basic pick-to-light systems utilize lights installed above the racks or bins in order picking areas. Based upon each order, a light will appear with a quantity to select. Pickers choose the item or items for the request, and push the illuminated indicator to confirm that the selection has actually been completed. When no more lights illuminate, it communicates to the picker that the shipment is done.
Light Pick Benefits
Storage facilities that execute pick-to-light systems can frequently achieve more than 450 picks per hour, per picker. This equates to a nearly tenfold improvement over warehouse pickers utilizing paper based methods. Here are a few other reasons warehouse managers may want to seriously consider the technology:
- 30-50% boosts in pick rate productivity
- 99.9+% accuracy rates
- Lowered order cycle times
- Higher throughput
- Lessened employee training time
- Superior customer service
- Reduced operational expenditures through decreased labor, errors, rework or returns
- Consistent picking processes
- Reduced costs through the elimination of paper picking lists
- An intelligent pick process with visibility into day-to-day metrics
Pick to Light Hardware
Although there are countless Pick-to-Light suppliers with differing solutions, the majority of systems utilize the following elements:
- Illuminated Signaling Lamps. This is how the system communicates with the operator. Light modules have an LED to indicate the location of the item and an item count display so the operator knows the number of products to select. Normally there is a confirmation button on the module that the operator pushes when a pick has actually been finished. Some light devices have bypass functions that enable pickers to increase or reduce pick quantities manually.
- Bay Displays. These alphanumeric display screens are positioned at each rack bay or pick zone. They signal order numbers, handling guidelines and other relevant details.
- Bus/ Duct Substrate. Many pick-to-light setups utilize a bus system that affixes to each rack face. These buses provide electricity and digital information to lamps and display screens. Each bus has an independent power and information feed, guaranteeing that the failure of a single bus does not bring down the entire system. Lights can be quickly positioned anywhere along the bus, so when SKU positions are revised the system can be reconfigured effortlessly.
Warehouse Picking Automation Consultants Near Me
To find out more on how you can introduce a pick-to-light system in your warehouse or distribution center, contact a Raymond West consultant today.
Raymond West's Fremont facility serves all of the Bay Area, including San Francisco, Oakland, San Leandro, Hayward, Union City, Fremont, San Jose, Santa Clara, Mountain View, Palo Alto, Redwood City, San Mateo, South San Francisco, Richmond, Vallejo, Concord, Pleasanton, Livermore and all surrounding areas.
Raymond West | San Francisco Bay Area Material Handling Equipment Supplier
41400 Boyce Rd
Fremont, CA 94538
(800) 675-2500