Pallet Racking Los Angeles
Pallet Racks
There are many types of pallet racking systems available today, and choosing among them depends on your warehouse space constraints, product flow requirements, selectivity needs and of course your budget.
It’s a good idea to look at your business requirements from time to time and make sure that your pallet racking system is right for your business. Even moderate sales increases or incremental product mix changes can have a significant impact on your warehouse requirements over the course of just a few years. A periodic review can give you an opportunity to identify efficiency gains, cost savings or both.
Many businesses have always used selective racking and have never considered other types of racking systems. In fact, many don’t know much about the other options that are available to them. This article is meant to be a high level overview of what’s out there and how different racking types can improve your warehouse efficiency and flow.
Selective Rack
Selective racking is what most businesses use today. It’s made up of uprights and beams, and pallets typically sit on cross bars. Selective rack is made of either structural and roll formed steel, with the latter generally being more versatile and less expensive, although not as robust as structural steel systems.
Most selective rack systems are single deep, meaning the bays are a standard 96” x 42”, all pallets are “first in / first out” since it’s a single row, and pallets are loaded and unloaded from the front of the rack.
Although less common, there are also double deep selective rack systems. These are usually “last in / first out” systems because these racks are still loaded and unloaded from the front. Generally, two pallets of the same product are stored in each bay to avoid moving the front pallet to get to the back one. Special deep reach lift trucks are required for double deep configurations.
There are also very narrow aisle (VNA) selective rack solutions that use special wire-guided or rail guided lift trucks. As the name suggests, the aisles for these systems are much narrower which increases warehouse density and provides for better space utilization.
Selective rack systems may very well be your best option, particularly if you have a quick turnover business and need immediate access to every product in the warehouse.
In general, selective rack is used because it allows direct access to a wide variety of products, it’s comparatively inexpensive and it’s easy to implement and reconfigure. However, it’s the lowest density option of all racking systems, so it may not always be your best option.
High Density Pallet Racking
Drive-in racking and, less commonly, drive-through racking systems are used for high density applications where many of the same items are stored together. They are ideal in situations where entire bays of products get moved at the same time.
These bays are generally at least four pallets deep, so a single bay that’s four pallets deep and four pallets high can store sixteen pallets. The racks that make up these bays are built without beams so that lift trucks can maneuver in and out. Pallets rest on rails that run along either side of the bay.
As the name suggests, drive-in racking systems allow the forklift operator to actually drive into the bay, place the pallet in the correct position and then reverse out. This is a “last in / first out” system that limits selectivity and access to products.
Similar to drive-in racking is drive-through racking which allows access to both sides of each bay. Drive-through storage is not as dense because it requires aisles on both sides of each bay, but it does allow for “first in / first out” inventory management.
Dynamic Storage Racking
There are two primary types of dynamic storage racking: pallet flow systems and push back rack systems. These are higher density than selective rack, typically two to five pallets deep and are somewhat more flexible than drive-in our drive-through racking.
Pallet flow systems are racking structures with aisles on both sides where pallets are loaded from the rear and travel down a slight incline via roller conveyors or skate wheels toward the front. As pallets at the front are removed, pallets in the rear move forward.
To compare pallet flow systems to the other options discussed here, each layer of these systems stores the same product, so they aren’t as flexible as lower density selective racking. As compared to other high density solutions, they do offer equivalent “first in / first out” capabilities to drive through systems but with much greater flexibility.
Push back rack systems are racking structures with a front side aisle where pallets are loaded from the front and travel up inclined rails via special nested carts. As each pallet is loaded from the front, it pushes the pallets behind it up the incline.
Like pallet flow systems each layer of a push back rack system typically stores the same product. In contrast to pallet flow racking, push back racking is a “last in / first out” configuration because all pallets are loaded from the front. This allows for higher density racking than pallet flow systems.
Where To Buy Pallet Racks In Los Angeles
If you’d like a full analysis of pallet racking options for your Los Angeles warehouse, you can speak with a professional at Raymond West by calling 562-944-8067.
If you’re anywhere in Southern California or Las Vegas, you can find us at these locations:
Los Angeles, CA
9939 Norwalk Blvd
Santa Fe Springs, California 90670
Phone: 562-944-8067
Ontario, CA
4602 E Brickell St.
Ontario, California 91761
Phone: 909-930-9399
San Diego, CA
12310 World Trade Dr
Ste 111
San Diego, California 92128
Phone: 858-679-1800
Valencia, CA
28309 Industry Dr
Valencia, California 91355
Phone: 661-206-0462
Las Vegas, NV
2555 E. Washburn Rd.
North Las Vegas, Nevada 89081
Phone: 702-651-6480
You May Also Like:
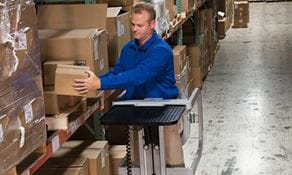
Aerial Lifts Los Angeles
Raymond West offers a full line of aerial lift options for your Los Angeles area business
Learn More
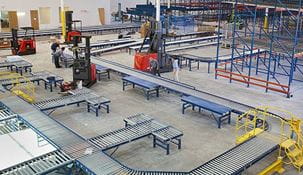
Conveyor Systems Los Angeles
Conveyors and AS/RS systems can increase the efficiency of your warehouse operations, improve safety and significantly reduce labor costs. We are your Los Angeles based warehouse automation experts.
Learn More
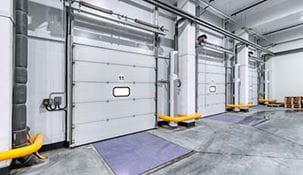
Dock Equipment Distributor - Los Angeles CA
Although it’s a simple device, a dock leveler is a critical piece of equipment. Every pallet going in or coming out of your facility goes across a leveler, so choosing the right option is an important decision. Here are a few things to consider.
Learn More
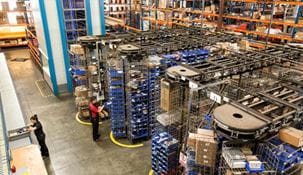
Material Handling Los Angeles
Raymond West offers a full line of warehouse equipment for your Los Angeles area operation
Learn More
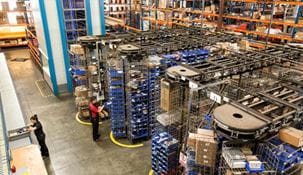
Warehouse Equipment - Los Angeles, CA
Automated storage and retrieval systems (AS/RS) options are revolutionizing the warehouse. Call Raymond West for a consultation on AS/RS implementation.
Learn More